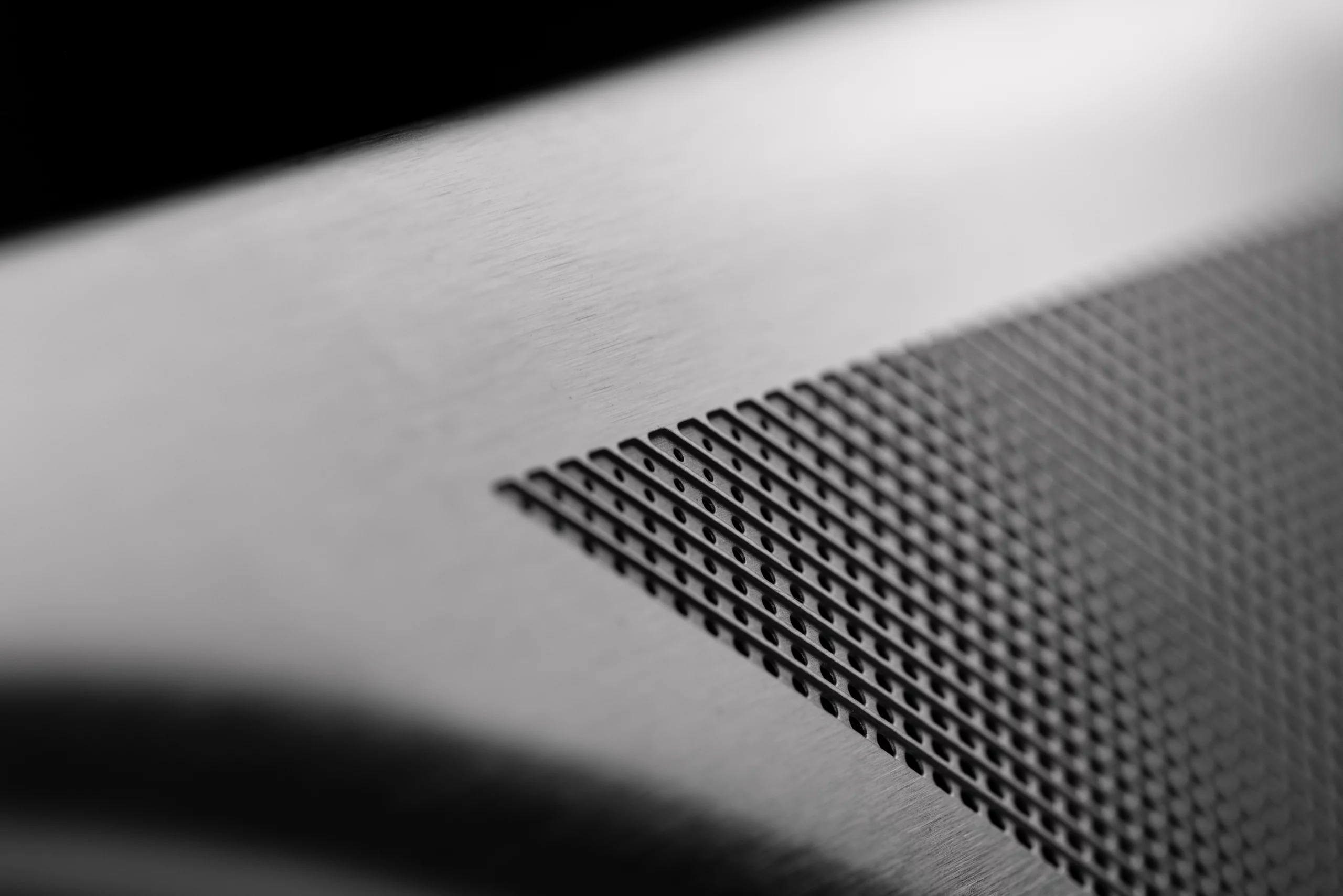
01 Apr Design Considerations for Interior Metal Components
When it comes to designing and developing automotive interior trim, talking to an experienced supplier with a deep understanding of the product can provide a better understanding of what is really needed. In this blog post, we will run through some of the key points that design engineers should consider when developing premium metal components.
Introduction
Traditionally, the roles of OEMs and tiered suppliers during the procurement process have been clearly defined. The OEM sends out a specification with an RFQ and the suppliers reciprocate with a pricing offer. While this has historically been a financial race to the bottom, OEMs are increasingly recognising the added value that can be created by specialist segments of the automotive manufacturing sector. A company that is hyper-focused on specific components or elements of a vehicle will usually have a better handle on that product line than an OEM looking at the bigger picture.
At Vestatec, our initial RFQ response will be to provide feasibility assessments based on the CAD data supplied, as well as advising on design for manufacturing using the historical experience of our engineering team.
In some cases, typically involving more complex form metal components, we put the customer CAD data through press-forming simulation software and use this to feedback any potential issues, such as locations of wrinkling tendency or splitting. We see it as our role to provide information to aid a feasible design at the RFQ stage as it helps build trust and allows more time to incorporate the required changes ahead of the design freeze. We will also determine which areas require optimisation loops to create a durable, high quality end product.
Any supplier worth its salt will offer these services, but we will go even further and provide consultancy that can lead to completely different materials used for these components.
Material World
There are a select few materials capable of achieving the desired end product when creating metal components for interior trim, including aluminium and stainless steel.
While aluminium is more commonly used, stainless steel provides a myriad of benefits better suited to the needs of the customer – especially on perforated components. Although it has a higher density than its aluminium counterpart, its corresponding strength offers the end user a more durable finished product and helps to reduce accidental damage to the installed components. This is a particularly common problem with large aluminium speaker systems positioned in the vehicle’s doors.
Moreover, untreated stainless steel has corrosion, scratch and abrasion resistance properties, which can only be achieved by putting aluminium through an anodising process. Furthermore, when stainless steel is coated with PVD, it can even mimic the desirable appearance of aluminium, but with the added benefits of stainless steel.
Despite the notable advantages of using stainless steel on perforated designs, aluminium is still the default material choice for many OEMs. If we receive an RFQ which specifies aluminium, we will typically undertake a detailed consultation with the customer’s engineering team to understand their requirements and ultimately determine the best solution for their desired outcome.
Of course, we are upfront about their options and the benefits of each, but when it comes to interior trim applications, the benefits of stainless steel generally bring it out on top. Sometimes the client will insist on a quote using their specified materials, and in these cases, we’ll also provide a quote based on our proposed materials for comparison.
As with any industry, keeping costs low while maintaining quality is always a priority, so it is part of our role as a valued supplier to make it simple for our customers by offering them quotes for both what they asked for and our alternative recommendations. Once they see the price comparisons and the benefits of the alternative approach, they usually decide to change tact.
Key Benefits
Cost is not the only consideration. Cabin aesthetics, particularly for high-end cars, are becoming increasingly important. Consumers always want a better driving experience, which starts the moment they get inside their vehicle. This is reflected in the booming demand for bespoke vehicles. Whilst we always engineer our parts to optimise their performance, we know that they also deliver a touch of luxury as decorative features within the cabin.
At Vestatec, our expertise is in the manufacturing of premium speaker grilles, as well as other interior decorative trim components. The typical assembly of our speaker grilles is a scrim – a polyester-based fabric positioned between a metal grille and a polymer support. The metal grille is the focus when it comes to aesthetics as this is the main component that is visible to the customers. It is chemically etched to create logos and hole patterns for sound transparency and decoration, press formed into shape, coated and then assembled.
PVD coating is a process well suited to stainless steel and provides a variety of different colours (e.g. black, silver, gold and blue)., The process involves vaporising a base metal, which is then deposited onto the metal grille to create a thin metallic coating less than a micron thick. Due to the coating being so thin, the surface finish of the substrate is incredibly important and can be used to provide a variety of different aesthetics. For example, OEMs can choose from a range of options, including brushed, matte or polished.
Furthermore, stainless steel chemically etches better than aluminium, achieving tighter tolerances, a greater level of surface detail and a higher gloss level giving the finished part an elevated aesthetic. Additionally, the combined costs for the material and etching is typically lower for stainless steel than aluminium.
Performance
As well as aesthetic design considerations, we must also factor in material properties and functional performance. Design engineers often have initial concerns about the weight of stainless steel – after all, the density of aluminium is approximately a third of the density of steel. However, to achieve equivalent dent resistance, a thicker aluminium sheet must be used. Additionally, unless you’re trying to squeeze every surplus gram out of a vehicle, it’s often a moot point. A typical stainless steel speaker grille – just the metal component – would weigh 43g. In a real-world application, switching to aluminium would save around 20g, which over a four-piece car set isn’t a huge weight saving. Therefore, overall, the advantages of stainless steel outweigh the additional mass it brings.
It’s also important to make design engineers aware of some other properties that can impact design, such as limitations on form depth. You cannot finish metal edges like you can with injection moulding; however, aluminium has its own flaws as it is prone to cracking in certain material grades or if processed through multiple forming stages. You can anneal between pressing steps to overcome this, but it is an added expense in cost and time. Even though stainless steel is less malleable, we can deliver a product that achieves the desired aesthetics whilst minimising surface defects.
Ultimately, the function of the speaker grille is to protect the speaker from foreign objects whilst maintaining audio transparency. At the early stages of design feasibility, we work to understand the customer’s requirements for audio transparency, which is usually stated as a percentage of open area with the metal grille and the polymer support. This is to ensure that their expectations are compatible with the pattern they have requested, without losing the overall durability of the component – so it really is a balance of function and fashion. The scrim material is also an important factor as some fabrics are less audio transparent than others, which can impede the sound quality of the speakers.
Design for Manufacture
Designing for manufacture tends to be an afterthought, so it is crucial that design engineers consider the manufacturing process early in the design phase. This includes design rules for chemical etching, such as minimum hole size and half etch features for a given material thickness and minimum radii for through etch features, as well as the feasible flange depth and flange angles required for press forming.
Similarly, consideration should be given to draft angles and split lines for injection moulding, and design engineers should give thought to the component’s suitability for fixturing during the coating process.
Design Trends
We’re also seeing a move towards greater aesthetic harmonisation across the metalwork within the cabin. This is reflected in requests to PVD coat a broader range of metal components, including door handles, dials and switches, to give them a decorative metallic finish and create colour harmony throughout the cabin. Non-decorative PVD coating is commonly used to add durability on various types of tooling and components in car engines and is even used frequently in Formula 1 and aerospace. Because it was developed for these demanding applications, the abrasion resistance is very good.
In addition, we’re seeing a trend to go larger with single components such as combining speaker grilles with the interior trim around door handles. Furthermore, we’re being asked to develop the etching process beyond just the transmission of sound. Many OEMs are now looking to transmit light into the cabin. We’ve seen this in several recent vehicle launches and believe light through metal will be a standout trend over the coming years.
Costly Errors
Ultimately, there are several considerations in manufacturing that a valued supplier can help OEMs resolve to achieve their desired interior trim components. In most cases, initial designs for interior parts in practice will wrinkle or a pattern will distort. By utilising simulation tools or rapid tooling methods for the area of concern – we can avoid costly mistakes further down the line.
Sorry, the comment form is closed at this time.