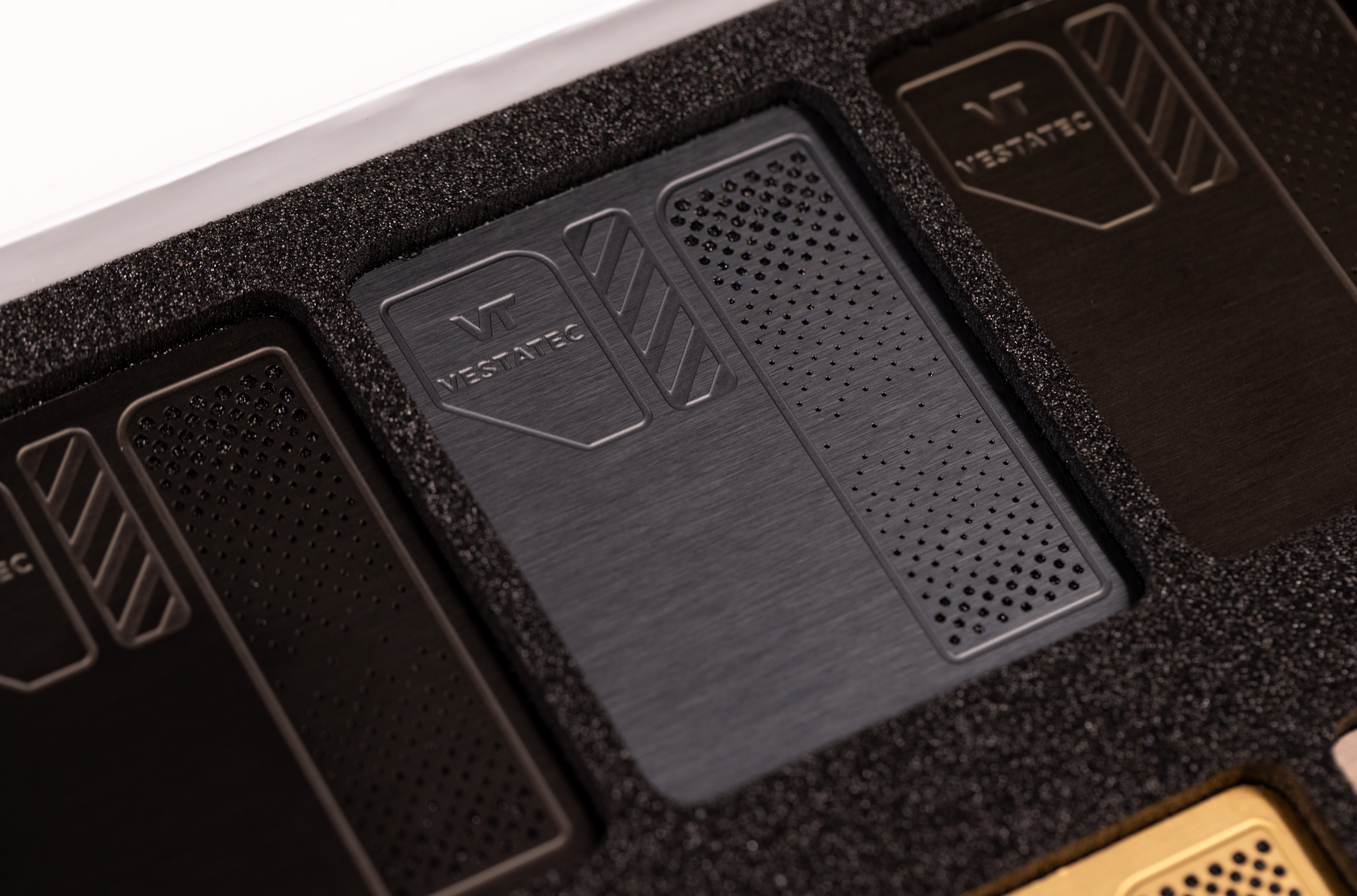
11 Nov Crafting Luxury: A Case Study
After more than two years of hard work developing some of the most complex interior components on the market, the team at Vestatec were delighted to see such a positive response to the mostly hotly anticipated car launch of 2024.
The vehicles in question, a Coupe and RHT platform of the same model, were debuted in Miami to critical acclaim. The OEM behind them is renowned for its craftsmanship and innovation, continually leading the way in luxury, engineering and design. With its distinctive Italian flair, the company is undoubtably the most recognisable car brand in the world.
The latest additions to its line-up were no different, serving as shining examples of automotive excellence. These vehicles embody a seamless fusion of cutting-edge technology and timeless elegance, setting new standards for performance and style in the luxury car market. Crafted by some of the most talented designers in the world, each vehicle is a masterpiece, ensuring that every detail meets the high standards its end-customers expect.
In this blog post, we will explore the collaborative role Vestatec played in supporting the design and development of a new generation of interior components, incorporating manufacturing techniques never previously used in the OEM’s vehicles.
It is a partnership that fused artistry and engineering, with the overarching goal of creating a cabin experience to match the thrill of the drive.
Striking collaboration
Our journey began with the Vestatec team making a pilgrimage to the OEM’s world-famous headquarters in Italy.
Here, in the birthplace of many iconic cars, the Vestatec team presented samples to representatives from styling, design and engineering, which showcased a vision of what the future of luxury automotive interiors could look like. Combining modern manufacturing techniques, such as chemical etching and PVD coating, this was an opportunity for Vestatec to show the intricacies of their components and demonstrate how to optimise for aesthetics and functionality.
Given the significance of the upcoming vehicle, which pays homage to a much-loved and iconic predecessor, the OEM sought a supplier driven by innovation and uncompromising quality in the development process, ultimately leading to Vestatec.
The right tools for the job
Crafted from premium 0.5mm/0.7mm brushed stainless steel, there were 18 unique grilles developed across the two platforms.
Each component starts with a single-stage chemical etch to create the desired hole pattern. Then, the parts are press formed into shape. Some of the grilles require multiple stages to achieve their complex form, with one component going through 5 levels of pressing.
The components are then PVD coated in either black or graphite, to achieve the desired metallic, jewellery like aesthetic. The largest of these parts is further accentuated by a chrome-plated bezel that framed the grille. The use of such high-quality materials and advanced manufacturing techniques ensures that each component not only meets but exceeds the customer’s stringent standards for durability and finish.
Every detail of the finished parts, from the elegant curvature of the door mid-range grilles to the pristine A-surface of the colossal door woofers, showcase Vestatec’s commitment to pushing the boundaries of automotive craftsmanship. Several assembly techniques were employed to ensure precision in construction, while careful consideration was given to switch and handle apertures, providing seamless integration and functionality. This attention to detail extended to the acoustic properties of the audio components, ensuring that the sound quality matched the luxurious feel of the vehicle’s interior.
Leveraging advanced software analysis tools and expertise, Vestatec’s engineers navigated technical hurdles precisely, ensuring that every component seamlessly integrated form and function. The use of these state-of-the-art tools allowed the team to optimise the performance and aesthetics of each component, overcoming potential issues before they could impact the production process.
These meticulous details underscore a shared vision, dedication and unwavering pursuit of excellence between Vestatec and its customer.
Collaborative approach
Max Bylina, Vestatec’s Business Development Director, reflected on the project, saying, “We took a consulting approach throughout the project, which was invaluable in guiding the OEM towards practical solutions without compromising on design integrity. Despite the complexities inherent in the manufacturing process, our dedication to excellence ensured that every challenge was met with innovation and ingenuity.”
The collaboration between the two organisations served as a driving force, with the parties overcoming several challenging obstacles to lay the foundation for a legacy of automotive excellence.
Max added: “As the vehicles debut, they stand as a testament to the customer’s vision, a vision we are honoured to bring to life, through our craftsmanship. Together, these automotive masterpieces represent the pinnacle of luxury, sophistication and engineering prowess. With our contributions, these vehicles continue the OEM’s reputation for redefining the boundaries of automotive excellence, setting new standards that will resonate for future generations.”
Sorry, the comment form is closed at this time.