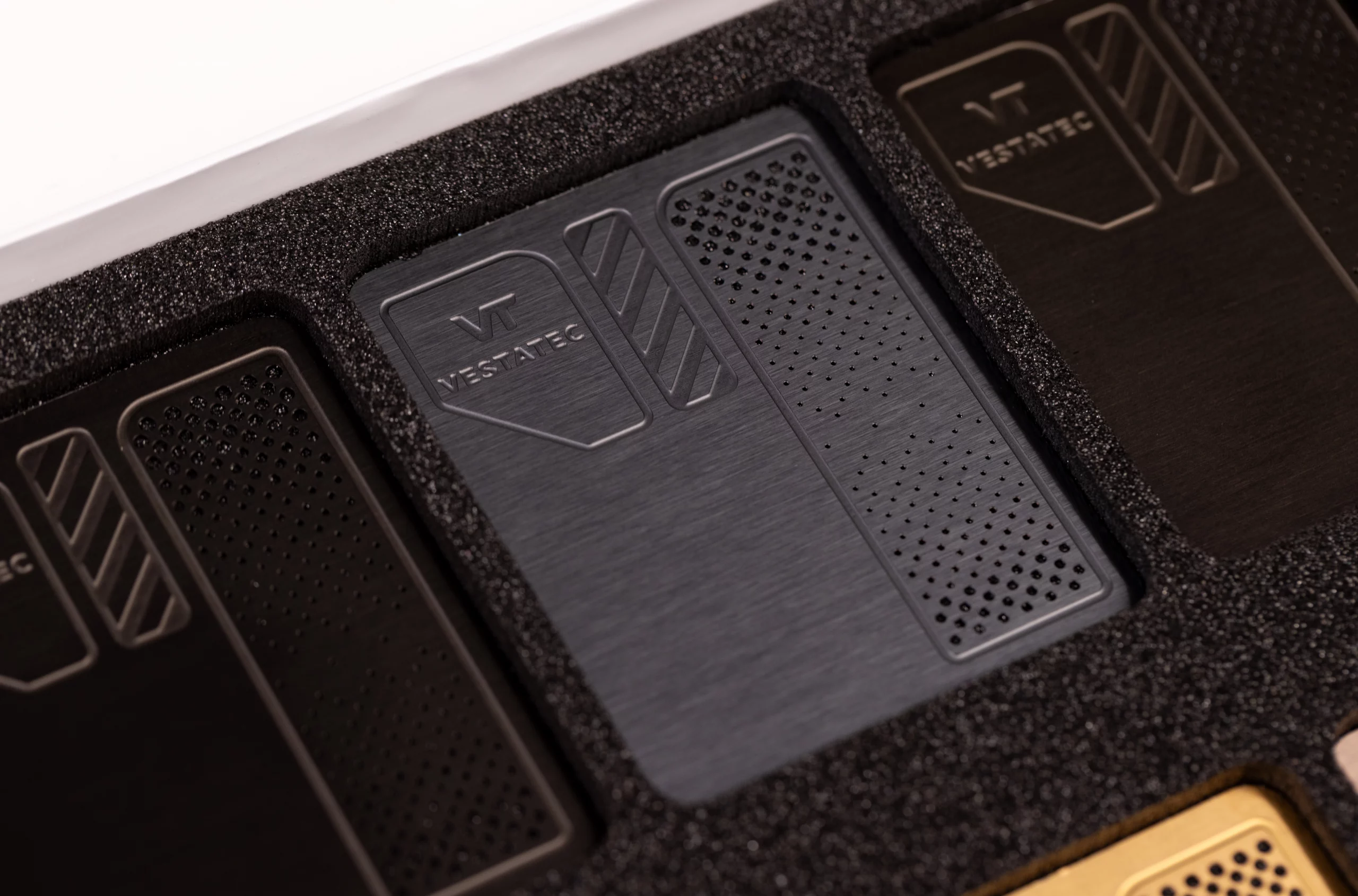
second slide
Physical Vapour Deposition (PVD) is an innovative form of metal coating that creates a finish which is durable, sustainable and aesthetically pleasing. At Vestatec, we are proud to be able to offer PVD coating in-house – giving you a one-stop-shop with a full spectrum of expertise in both metal forming , coating and assembly.
Our PVD coating services are driven by detail and can truly redefine your metal components. Begin your journey with us by getting in touch below:
The PVD coating process is a highly advanced technique which is designed around delivering a durable and aesthetically pleasing end product.
To prevent defects, all products pass through our extensive cleaning line before coating. This process includes tanks for cleaning, rinsing and deionising. After cleaning, the products are dried and air deionised.
Coating begins by placing the metal components into a vacuum chamber inside a cathodic arc PVD machine.
Within the machine, a compound is created and applied atom-by-atom to the component by allowing an electrical arc to vaporise a conductive metal target source and combining it with a combination of gases.
The process is never complete without rigorous and highly focused testing which ensures a consistent level of high-quality.
Coatings made to <2 μm maintains the substrate surface finish for good durability.
Low per-part coating cost. Being in-house improves cost and time efficiency.
There is a range of surface finishes available, including brushed, polished and matte.
An environmentally clean process that produces no hazardous waste.
High durability with good scratch and wear resistance.
Multiple colours are available, including true black and bespoke shades.
Customers we proudly work with
To learn more about how PVD coating can revolutionise your metal components, get in touch.